材料を2つ以上に分割する工程です。大きくは切断加工とせん断加工がありますが、当社では切断加工をメインで使っています。丸ノコ刃や帯ノコ刃で材料を削りながら切りますので、ノコ刃の厚み分の切り代が必要となります。
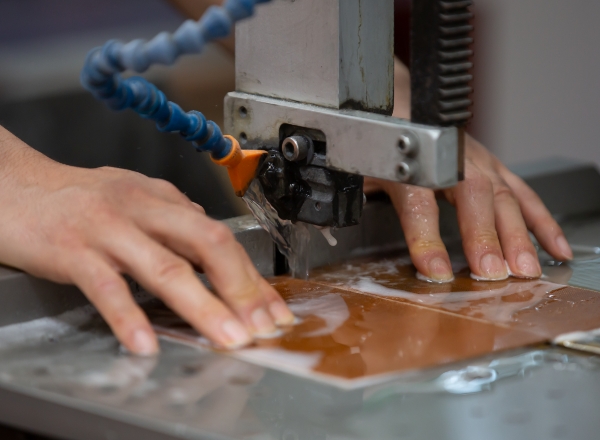
ほとんどの場合、加工の第1工程となりますので、樹脂加工レスキュー工場では板材切断用にパネルソーを2台、丸棒切断用にバンドソーを1台設備しています。その他、曲げ加工後や追加工時に切断が必要な場合、横切り盤やジグソーなどを使う場合があります。
樹脂加工レスキュー工場では、ダイヤモンドバンドソーを導入しており、CFRPなどの硬い素材の切断にも対応しております。
材料を曲げる工程です。大きくは熱間曲げと冷間曲げがあります。冷間曲げは薄くて靭性がある材料、熱間曲げは厚くて靭性が無い材料を曲げる際に採用します。樹脂加工レスキュー工場では熱間曲げがメインとなります。熱間曲げには大きく部分加熱と全体加熱があります。
部分加熱は板やパイプの必要な部分のみ加熱して軟化させて曲げる方法です。加熱方法は管ヒーターやホットジェットなどを使用します。使用する治具も簡易的なもので比較的手軽な工法です。
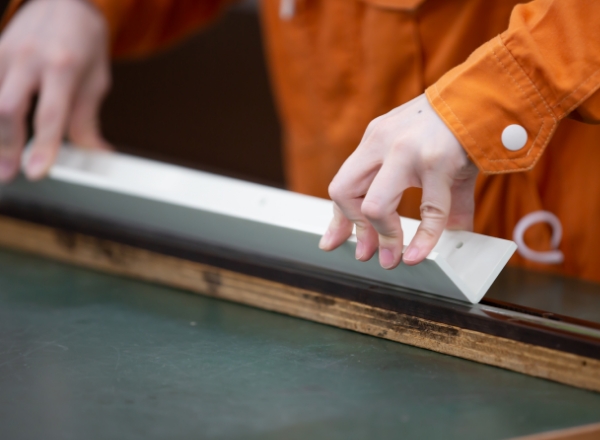
全体加熱は板全体を加熱して成形する方法で、木型や金型が必要となります。加熱は材料全体を加熱する炉が必要となり、樹脂加工レスキュー工場では、温度管理が簡単な電気炉を使用しています。また、木型も社内で製作する為、より精度の良い成形を可能にしています。
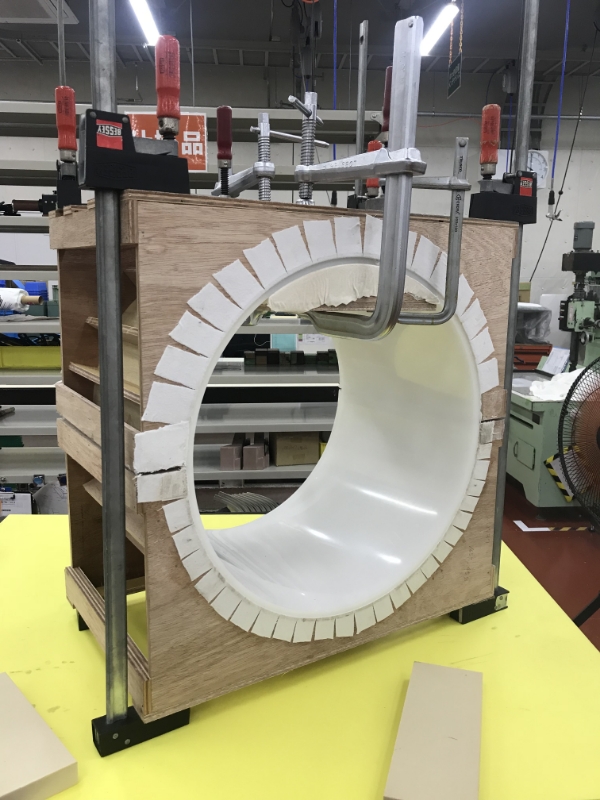
※内製はプレス成形のみです。真空成形等はパートナー企業で対応しております
2つ以上の材料をつなぎ合わせる工程です。ネジ止めなどの機械的締結以外に、接着と溶着の工程があります。樹脂加工レスキュー工場では、接着は二つの材料の間に接着剤を媒介とした結合、溶着は材料そのものを化学的乃至は熱的に溶かし材料同士の結合と定義しています。
(一般的には諸説あります)
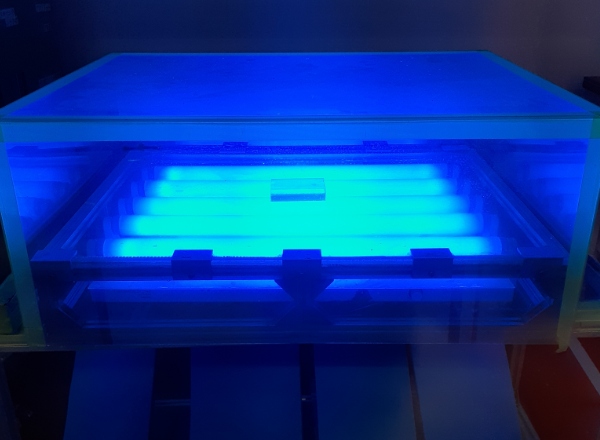
瞬間接着剤やエポキシ系接着剤、珍しいところでは重合接着や光接着にも対応いたします。材料と接着剤の相性によりその強度は異なりますが、溶着より強度が劣ります。エンプラやスーパーエンプラは接着が困難な材料が多い為、機械的締結をお勧めしております。
大きくは化学溶融型接着=溶剤接着(ここで接着が出てくると分かりにくいですが)と熱的溶着に分かれます。溶剤接着は、有機溶剤を用いて材料を溶かして接合する方法で可能な材質が限られます。
(別表参照)
熱的溶着の中でも樹脂加工レスキュー工場で主流なのはホットジェット溶接と呼ばれる工法です。これは二つの部材を外部から熱風で溶かした溶接棒で接合する方法です。これも可能な材質が限られます。
(別表参照)
※材質と形状によって接合強度は異なりますので、ご相談ください。
溶着は、機械化が進んだ今日とはいえ人間の技量に負うところが大きく、接着強度や溶接強度を実製品から計測して保証する事が出来ません。その為、弊社では熱風溶接作業、溶剤接着作業を「特殊工程」と位置づけて、当社の認定した作業者のみが作業をしています。溶接作業者の認定にはJIS Z 3831プラスチック溶接技術検定における試験方法及び判定基準を用いて1年に1度技術認定を実施しています。
材料の余分な部分を除去して形状を得る工程です。大きくは穴あけ、旋削、フライスの工程があります。樹脂加工レスキュー工場では、様々な材料に挑戦してきた経緯があり、硬いものではCFRP、軟らかいものではショアA10のウレタンゴムを削ることができます。
材料にドリルなどの回転工具をあてて穴をあける加工です。一般的なドリルを使用したボルトを通すための穴や座ぐり穴、リーマーやボーリングバイトを使用した位置決めの為のノック穴や回転部を受ける為の軸受け穴、タップ等を使用したネジが切られたネジ穴など、精度や形状も様々です。使用する機械もボール盤をはじめとして、旋盤、フライス盤、マシニングセンター、電動ドリル等の手工具もあります。
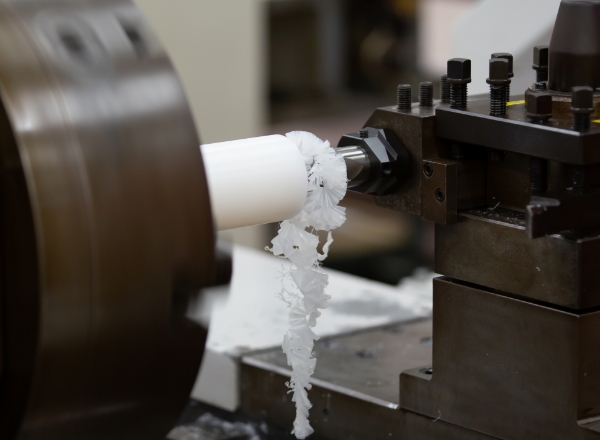
回転する材料に固定した刃物をあてて削る加工です。イメージとしては陶芸のろくろで、粘土が材料、手やヘラが刃物となります。この原理上、丸ものと呼ばれる円筒形状の加工品に多く使われる工程です。円筒部の端面や外径、内径を削って形状を得ます。ローレットと呼ばれる滑り止め形状や雄ネジであるボルトを加工する事もできます。使用する機械は旋盤がメインですが、樹脂加工レスキュー工場では5軸加工機は全て旋削にも対応しています。
固定した材料に回転する刃物をあてて削る加工です。イメージとしてはコーヒーミルで、いらないところを刃物で砕いて必要な形状を得ます。フェイスミルやエンドミル、サイドカッターなどの工具を使い、フライス盤やマシニングセンターで加工をします。先が丸くなったボールエンドミルを使用することで、3次元形状の加工をすることもできます。樹脂加工レスキュー工場では、全てのマシニングセンター、5軸加工機でCAD/CAMと呼ばれるソフトウェアを用いてNCデータを作成しています。3次元形状や高精度加工もお任せください。用する機械は旋盤がメインですが、樹脂加工レスキュー工場では5軸加工機は全て旋削にも対応しています。
製品表面を整える処理をする工程です。大きくは研磨、艶出し、加飾、洗浄の工程があります。
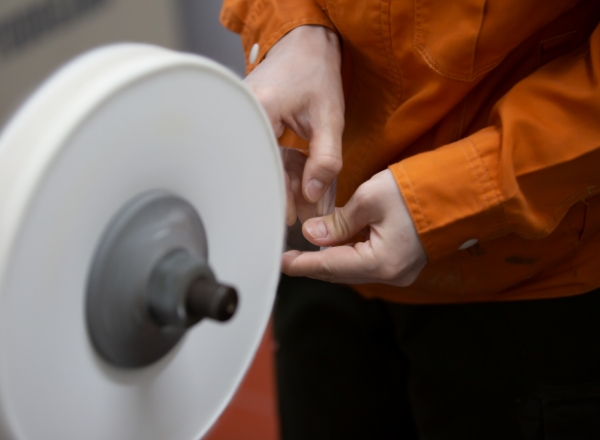
ペーパーやブラストなどで表面を粗らしたり、コンパウンドやダイヤモンドペーストなどで表面を磨いたりする工程です。樹脂加工レスキュー工場では、樹脂・プラスチック専用のメディアを使用したブラスト加工機を設備して、部品表面を親水化する処理が可能です。また、アクリルやポリカーボネートなどの透明素材を切削した後、バフ研磨やダイヤモンド研磨をして、レンズなどを製作したりしています。
研磨はほとんどが手作業になりますので、大変な工数がかかりコストが高くなる傾向があります。単に透明度が欲しいという場合は、ガスがけや溶剤による艶出しで対応する場合があります。切削目は残りますが、表面が滑らかになり透明度を上げる事ができます。
墨入れや刻印などは内製で実施しますが、シルクスクリーン印刷やパッド印刷、そして塗装は信頼できる協力企業にお願いしております。外装部品などは表面の意匠まで一貫して対応いたします。
製品は形を作っただけで終わりではありません。お客様がすぐに使用できるよう、綺麗な状態で納品いたします。アルコール清拭や水洗いはもちろん、細かい形状の製品は自作の超音波洗浄機で洗浄した後、汚れが付かないよう梱包をします。
(但し、使用している水は純水ではありません)
更に精密な洗浄が必要な場合には、専門の協力企業に依頼して対応することも可能です。
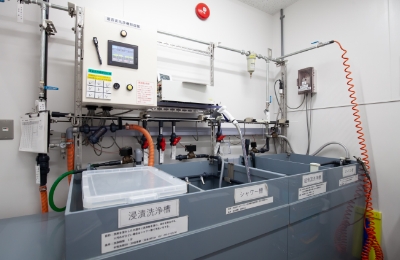